This Is How Aircraft Gas Turbine Air Pollution Can Be Reduced!
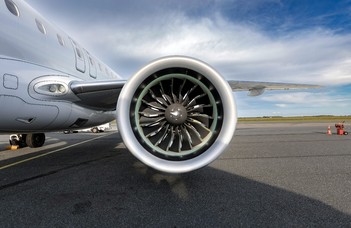
Passenger airplanes with a capacity of more than ten passengers, as well as almost all cargo planes, operate using gas turbine engines. Similarly, gas turbines power propeller-driven aircraft, helicopters, and frequently larger ships. A substantial portion of electricity generation also relies on gas turbines. The fastest-growing sector is aviation: international air traffic doubled between 1990 and 2019. The growth was curbed by COVID-19 only for two years, and following the pandemic, air traffic has been expanding at a rate of 3.7% per year (Transp. Res. D: Transp. Environ. 127 (2024) 104055). Currently, international air traffic consumes approximately 300 million tons of kerosene annually, with aircraft emitting 600,000 tons of CO and 3.6 million tons of NO into the atmosphere (Environ. Res. Lett. 19 (2024) 054019). The emitted nitrogen oxides cause photochemical smog and acid rain, and contribute to the depletion of the ozone layer. In modern gas turbines, most nitrogen oxides are formed in high-temperature regions (so-called “hot spots”) of the combustion chamber from the nitrogen molecules of the air. However, by modifying the operation of gas turbines, a significant reduction in nitrogen oxide (NOx) emissions can be achieved.
The Combustion Research Group at BME’s Faculty of Mechanical Engineering, led by Associate Professor Viktor Józsa, has developed a method to prevent the formation of such hot spots during combustion, ensuring a uniform burn throughout the entire combustion chamber. Their concept was validated through laboratory experiments conducted at atmospheric pressure, in which they burned aviation kerosene and measured the NO, CO, and CO₂ concentrations in the exhaust gas.
Figure 1: Flame in the experimental combustion device at BME. The high temperature of the flame front is due to the concentrated heat release.
Figure 2: Combustion filling the entire combustion chamber in the experimental combustion device at BME. The input power from the fuel is the same, but the temperature is not extremely high at any single point. Heat is released almost uniformly throughout the entire volume.
For years, the Chemical Kinetics Laboratory at ELTE Institute of Chemistry, led by Professor Tamás Turányi, has been developing computer models that allow for more accurate predictions of nitrogen oxide formation during combustion. Using computer simulations, the ELTE researchers successfully reproduced BME's laboratory results, then calculated the concentrations of NO, N₂O, and CO in the exhaust gas by varying the residence time and pressure using the same model. The pressure was varied between 3 and 60 bar, covering the entire typical pressure range from micro-gas turbines’ combustion chambers to the most advanced jet engines. The calculations indicated that it is possible to achieve operating conditions in aircraft gas turbines where the concentrations of all three pollutants in the exhaust gas are significantly lower than in currently used gas turbines. Therefore, this new method of avoiding “hot spots” can be successfully applied in aircraft gas turbines to reduce environmental impact.
More information:
Website of the Chemical Kinetics Laboratory of ELTE
Website of the Combustion Research Group of BME
The original article:
Janka Borsó, Máté Papp, Viktor Józsa, Tamás Turányi: Modelling of JP-8 distributed combustion using a HyChem mechanism under gas turbine conditions, Results in Engineering, 23, 2024, 102596 (https://doi.org/10.1016/j.rineng.2024.102596)